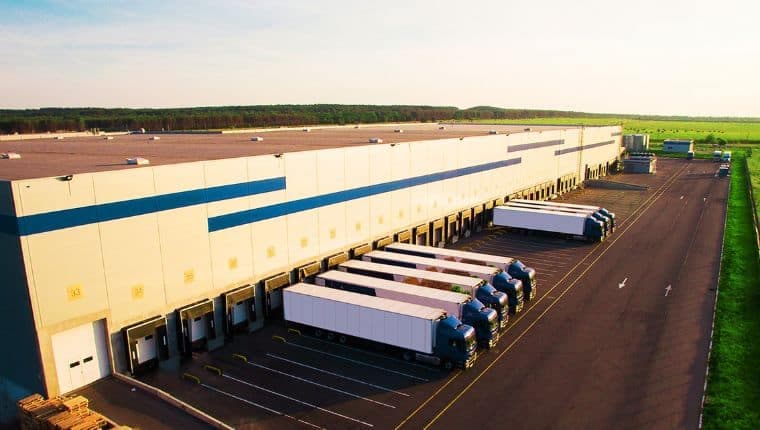
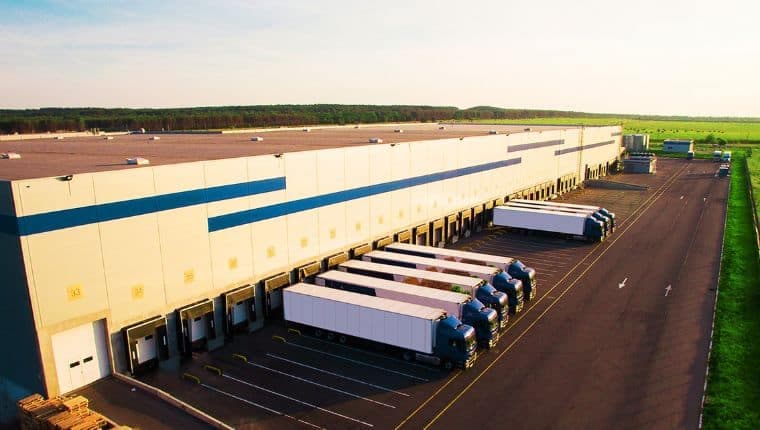
How to Integrate Cross-Docking into Your Supply Chain
The problem? Well, most people don’t design their entire supply chain around cross-docking. Usually, companies adapt their existing structures to the new paradigm. But is it really that easy, and what should companies do to integrate cross-docking into their supply chain seamlessly?
In this guide:
- Types of Cross-Docking
- Assessing Suitability for Cross-Docking
- Key Steps in Integrating Cross-Docking
- Considerations for Successfully Implementing Cross-Docking
Types of Cross-Docking
Cross-docking logistics are relatively simple to understand. It’s all about timing the incoming shipments just right so there’s enough time to unload and load them onto an outgoing transport without requiring any storage time.
When everything goes right, the system works like clockwork. However, companies have a choice to make. There are two types of cross-docking:
- Pre-distribution cross-docking means that the products are already sorted with predetermined distribution instructions before even reaching the cross-docking facility. This approach requires meticulous planning and efficient execution.
- Post-distribution cross docking is different. Instead of planning every move ahead of time, products are sorted and allocated to a cross-docking terminal based on real-time decisions about product allocation. This provides the benefits of warehouse storage without having to keep an extensive inventory in stock. However, it can lead to issues if there’s not enough stock to cover the downstream demands.
Assessing Suitability for Cross-Docking
To assess if cross-docking fits your logistics strategy, start by evaluating your product characteristics and supply chain dynamics. Ideal products for cross-docking are high in demand, predictable in volume, and require minimal handling. Ensure your supply chain exhibits reliable supplier schedules and consistent shipment arrivals, as cross-docking depends heavily on precise timing.
Review your technological capabilities; robust tracking and logistics software is crucial for managing the seamless transfer of goods at the docking terminal. This includes real-time data sharing among all parties to optimise goods flow.
Finally, consult with your team to verify the feasibility of integrating cross-docking into your existing operations, choosing between pre-distribution or post-distribution methods based on your precision and operational readiness.
Key Steps in Integrating Cross-Docking
Solving cross-docking logistics is mostly dealt with during the initial integration stages. Taking the time to inspect your existing supply chains and plan how cross-docking will fit in is critical to long-term success. Follow these steps:
-
Assess and Audit the Current Supply Chain
Look closely at your existing supply chain. Maybe you rely on warehouses for your logistics or operate something like a just-in-time supply chain. Whatever your set-up, it’s important to reimagine the existing pieces from a cross-docking perspective.
Moreover, you’ll want to audit your current supply chains to identify the issues with the present set-up. Working with your team, find solutions to these issues using cross-docking.
-
Choose the Best Facility
Cross-docking relies on a fast and efficient facility capable of unloading goods from one delivery and rapidly loading them up onto an outbound transport. There should be minimal storage time; otherwise, it defeats the point of the logistics system.
Carefully consider the different facilities available. You won’t need the same excess storage space for long-term product storage. Instead, look for facilities that can be set up to efficiently and effectively unload and load up lorries without any issues. The faster this can occur (without mistakes), the better the system will run.
-
Implement WMS & TMS Systems
Of course, it’s not just the facility itself that matters. Crucial to cross-docking logistics are the warehouse management system (WMS) and transportation management system (TMS).
The WMS tracks all inventory within the distribution centre, helping to coordinate tasks, reduce manual processes, and boost order fulfilment accuracy. The TMS, on the other hand, helps improve the delivery of goods, planning the best delivery routes, reducing shipping costs, and optimising load building. Depending on whether you run a pre- or post-distribution cross-docking facility, how you integrate your WMS and TMS systems will differ. Pre-distribution facilities may not need to keep as close an eye on current inventory levels, as products move rapidly from one lorry to another (prioritising the TMS system), whereas post-distribution facilities will need to understand where a specific product is going, meaning the WMS is essential.
-
Process Mapping
Map every step of your intended cross-docking process to identify potential bottlenecks and streamline operations. Visualising the flow from incoming shipments to outgoing transport ensures a clear understanding of each touchpoint, enhancing efficiency and reducing transition times between stages. This crucial planning phase helps tailor the logistics to your specific operational needs.
-
Stakeholder Management & Team Training
Everyone needs to understand your new system to the letter. The final step in integration is managing stakeholder expectations and informing them of what to expect. You then need to train your team thoroughly on the system, software, and scenarios that can occur. The better everyone is drilled, the fewer issues will occur.
Considerations for Successfully Implementing Cross-Docking
Cross-docking logistics aren’t an automatic solution to your distribution problems. You need to calibrate this new system to your specific business, whether it’s shipping time-relevant food products or game consoles in time for Christmas.
Here are some considerations:
- Inbound vs. Outbound Coordination. One of the key metrics for cross-docking logistics is the speed at which products go from inbound to outbound transportation. You want each transport to arrive at the right time to give your team a chance to unload, organise, and load up each lorry.
- Inventory Visibility. How much inventory visibility do you need? This is the responsibility of your WMS. If you’re operating in a post-distribution system, then it’s crucial you know how much inventory you have as you’ll have to organise where it’s going next.
- Supplier Relationships. Working hard on supplier relationships doesn’t just get you a discount. You want excellent communication to know when your deliveries are going to arrive.
- Quality Control. Mistakes will cost you. It’s not just about fast transit times. It’s all about avoiding mistakes. Keep a close eye on the accuracy of your order fulfilment to see if there are issues with your system.
Check out MIXMOVE’s X-Dock Warehouse Management Software if you’re looking to streamline your cross-docking processes. It’s specifically designed to integrate smoothly with your current systems, providing real-time insights that help you make smarter decisions and streamline your operations. Whether you’re focusing on pre-distribution or post-distribution models, X-Dock is built to optimise your logistics, improve efficiency, and reduce costs. Request a free demo to learn more.
MIXMOVE is a state of the art event-based platform, providing cloud software that supports logistics by connecting systems, increasing profitability and reducing C02 emissions. For more than 10 years, we have given shippers, carriers, forwarders and logistics service providers the best customer experience in getting logistics transparency, predictability and resilience. We’ve helped customers such as 3M reduce their transport costs and emissions in their network.